Regulagens da colhedora de trigo
Leia sobre cuidados e regulagens da colhedora durante a colheita do trigo.
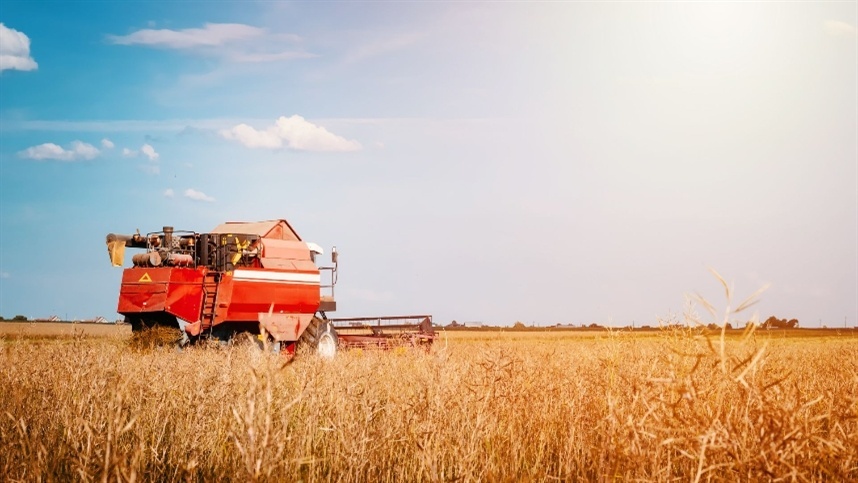
A colheita é uma etapa da produção que merece muita atenção, pois influencia tanto na produtividade quanto na qualidade final do grão. Durante esse processo, diversos cuidados devem ser tomados para reduzir as perdas, sejam elas em quantidade ou em qualidade:
- Iniciar a colheita com uma velocidade baixa até sentir e dominar as funções da colhedora. Pode-se aumentar aos poucos a velocidade, observando os resultados, até encontrar uma velocidade adequada, que se situa entre 3 km/h e 5 km/h.;
- Ajustar a colhedora conforme o manual;
- Colher uma área com tamanho determinado para quantificar as perdas;
- Verificar constantemente os grãos no tanque graneleiro, na retrilha, e a palha nos saca-palhas para verificar o funcionamento da trilhadora. Ajustar, se necessário, a rotação do cilindro e abertura do côncavo;
- Quando alterar algum ajuste, comprovar a perda de grãos;
- Verificar o ajuste da altura, velocidade e posição do molinete conforme as condições do grãos e velocidade da colhedora;
- Ajustar o fluxo e quantidade de ar e/ou peneiras quando houver perdas nessa área ou forem observados grãos sujos no tanque graneleiro;
- Evitar velocidades altas para não sobrecarregar a colhedora, evitando perdas.
Regulagem conforme a umidade do grão
A medida que a colheita vai sendo feita, as condições de umidade do grão e da palha variam, sendo necessárias novas regulagens;
- Umidade do grão em 13%: os grãos de trigo devem ser colhidos com a umidade ao redor de 13%, o que permite uma folga entre o cilindro e côncavo de 8 mm a 10 mm, e rotação do cilindro a 950 rpm.
- Umidade do grão em 16%: para a colheita dos grãos nessa umidade, a regulagem ideal requer uma folga entre o cilindro e o côncavo com 6 mm a 7 mm e aumento da rotação do cilindro para 1.100 rpm.
- Se a colheita for feita com uma umidade de 20% nos grãos, visando escapar de chuvas na maturação ou outros problemas, a regulagem deve ser cuidadosa. Nesse caso, a folga entre o cilindro e o côncavo deve ser de 6 mm, e a rotação do cilindro 1.300 rpm.
Apesar do trigo ser preferencialmente colhido com umidade mais baixa, a colheita com umidade mais alta permite algumas vantagens, como liberar a área para o próximo cultivo e menor possibilidade de ataque de pragas e doenças.
% de umidade no grão | % de grãos danificados |
33,4 | 10,3 |
29,4 | 7,3 |
23,4 | 2,7 |
20,3 | 1,0 |
18,4 | 1,0 |
15,8 | 0,5 |
Fonte: Vas e Harrison (1969).
As colheitas de trigo podem começar com umidades próximas de 18%, visando evitar danos aos grãos colhidos. Para colher em umidades maiores, podem ser feitas algumas alterações na trilha e cilindro / côncavo. Observe a tabela abaixo:
Umidade do grão (%) | Rotação do cilindro (rpm) | Folga cilindro - côncavo (mm) | ||||||||
24,7 | 19,6 | 16,3 | 13,0 | 1140 | 1260 | 1400 | 3,0 | 6,0 | 9,5 | |
Germinação (%) | 79,4 | 91,9 | 92,1 | 87,8 | 89,3 | 88,4 | 85,8 | 85,8 | 89,3 | 88,2 |
Dano visual (%) | 1,3 | 0,6 | 0,6 | 1,9 | 0,7 | 1,2 | 1,5 | 1,2 | 1,0 | 1,2 |
Fonte: Vas e Harrison (1969).
Pela tabela podemos observar que as condições de germinação e dano visual no grão de trigo são melhores nas menores rotações do cilindro, com umidade de 16% a 20% e folga do cilindro-côncavo de 6mm.
Regulagens da colhedora no trigo
Plataforma de corte
Acoplada a colhedora, é responsável pelo corte e recolhimento do trigo no campo, e é composta por: separadores da plataforma de corte (dividem longitudinalmente a faixa de cereal a cortar), molinete (conduz as plantas, levando-as para a barra de corte), barra de corte, cilindro caracol (direciona o trigo para o centro da plataforma) e esteira transportadora (trigo transportado para o sistema de trilha). Vejamos abaixo algumas regulagens:
Barra de corte: a barra de corte é composta por navalhas, contranavalhas (dedos), placas de desgaste e clipes. As navalhas devem estar afiadas e reguladas, já as contranavalhas (dedos) protegem as navalhas e servem como guia. As placas de desgaste podem ser ajustadas para compensar o desgaste da barra de corte, e as dobras devem estar alinhadas entre si, proporcionando o encosto em toda extensão da barra de corte. Também existem clipes fixadores que mantêm a navalha próxima da contranavalha, podendo ser ajustados conforme as navalhas se desgastam. Quando o corte não é perfeito, a barra irá vibrar o colmo da planta, causando perdas na plataforma de corte.
Molinete: conduz as plantas contra a barra de corte, e depois para o caracol de alimentação. A cultura deve ser movida de forma uniforme. Quando a lavoura de trigo possui um padrão normal, o eixo do molinete deve ficar deslocado entre 15 cm e 20 cm na frente da barra de corte. Caso as plantas de trigo estejam muito altas, adianta-se o molinete, porém, caso as plantas de trigo estejam muito baixas, o molinete é direcionado para perto do sem-fim.
Já na posição vertical, geralmente a ponta do dente do molinete fica em uma altura de 5 cm a 10 cm abaixo da espiga mais baixa. Caso haja plantas acamadas, o molinete deve ser deslocado para a frente da barra de corte.
Quanto à velocidade do molinete, esta se relaciona com a velocidade de avanço da colhedora. Essa relação se chama "índice de molinete (IM)", e se apresenta através da seguinte fórmula:
No trigo, recomenda-se os seguintes índices de molinete:
- Lavoura alta e densa: IM = 1,0 (molinete com velocidade igual à velocidade de avanço da colhedora)
- Lavoura normal: IM = 1,15 - 1,25 (15 a 25% mais rápido que a colhedora)
- Lavoura baixa e rala: IM = 1,35 (35% mais rápido que a colhedora.
Quanto à inclinação dos dentes do molinete, em lavouras densas com plantas altas, os dentes devem estar em posição vertical ou levemente inclinados para a frente. Já em lavouras com plantas de porte normal, os dentes devem ficar em posição vertical. Já em lavouras com plantas acamadas, os dentes devem estar inclinados para trás. Os dentes devem passar em cerca de 2,5 cm da barra de corte.
A rotação do molinete deve ser aumentada de forma que os dentes levantem as plantas antes dessas serem cortadas pela barra de corte. Porém, em lavouras com plantas bastante acamadas, recomenda-se usar dedos levantadores que erguem as plantas e guiam-nas para a barra de corte.
Regulagem do sem-fim do caracol
Para lavouras com plantas de porto normal, recomenda-se um espaço de 8 mm a 15 mm entre a base da plataforma e as roscas do sem-fim do caracol. Para lavouras densas, recomenda-se um espaçamento de 10 mm a 20 mm. As travas do embocador devem ser reguladas de forma que as barras da esteira transportadora fiquem em uma altura entre 10 mm e 12 mm do fundo do embocador.
Sistema de trilha
Trilhar consiste em retirar os grãos das espigas. No sistema de trilha, mais de 70% dos grãos são separados, sendo o resto separados nas demais unidades. A trilha pode ser feita por fricção, através do cilindro e côncavo. A abertura entre o cilindro e o côncavo pode ser regulada a depender da densidade de alimentação, umidade do grão e da massa de produto. Esta abertura afeta a qualidade da trilha e quantidade de grãos que é separada da palha. Para o trigo seco, recomenda-se a separação entre cilindro e côncavo de 20 mm na frente e 15 mm atrás. Para o trigo úmido, 10 mm na frente e 7 mm atrás, respectivamente.
Quando a trilha não ocorre de forma adequada, pode ser reduzida a abertura entre o côncavo e o cilindro, tornando mais delgada a camada de palha, fazendo com que a maior parte das espigas entrem em contato com o cilindro, ocorrendo uma ação mais eficiente na trilha.
Quanto à velocidade do cilindro, esta afeta o rendimento tanto na qualidade quanto na quantidade. Geralmente são usadas velocidades de 24 m/s para trigo seco, e 35 m/s para trigo úmido.
O excesso de trilha pode ser causado por alta rotação do cilindro ou por espaçamento pequeno entre côncavo e cilindro. Caso esteja ocorrendo alta rotação, recomenda-se reduzir 5% da velocidade e verificar os resultados. Caso seja diminuída em até 10%, abrir ligeiramente o côncavo. Caso o problema ainda persista, reduzir a velocidade de avanço da colhedora.
A falta de trilha ocorre por baixa rotação do cilindro ou por abertura excessiva entre o cilindro e o côncavo. Dessa forma, aumentamos a rotação do cilindro em 5%, e, caso o problema ainda persista, diminuímos levemente a abertura entre o cilindro e côncavo. Em situações de pouca palha estes procedimentos podem não ser o suficiente, sendo recomendado o aumento da velocidade da colhedora.
Já no saca-palhas, a oscilação deste deve sempre estar regulada com o volume de palha. Quanto mais palha, maior a velocidade de oscilação. A cortina é posicionada sobre o saca-palhas, e evita retardar o fluxo dos grãos, proporciona maior tempo para soltar grãos da palha e evita que grãos sejam lançados para fora do equipamento pelo batedor. Caso não haja necessidade de retardar o fluxo de palha, a cortina fica na posição indicada. Porém, em situações de colheita com a palha úmida, a cortina deve ficar solta. Caso ocorra bastante dificuldade de separação do grão da palha, pode-se utilizar uma cortina adicional.
Quanto ao sistema de limpeza, este é formado pelo ventilador e peneiras superior, inferior e de retrilha, e é responsável por remover os resíduos de palha. A peneira superior deve ser regulada de forma que o fluxo de ar separe a palha do grão, fazendo com que esta não passe para a peneira inferior. Caso a peneira superior esteja muito aberta, a peneira inferior ficará sobrecarregada. Já se a peneira superior estiver muito fechada, a retrilha fica carregada de grãos, e ocorrerão muitos grãos quebrados no tanque graneleiro. Além disso, a peneira pode ser ajustada em três posições: horizontal, média e alta. Utilizar a posição horizontal quando a alimentação é abundante, e, conforme diminui a quantidade de material que entra, a posição da peneira deve ser elevada progressivamente, até obtermos uma camada de material uniforme em toda a peneira.
A extensão da peneira superior tem função de recuperar pontas de espigas ou espigas que não foram completamente trilhadas, levando-as para a retrilha. Sua abertura deve ser um pouco maior que a peneira superior.
A peneira inferior separa todos os restos de palha dos grãos. Quando está muito aberta, surge bastante palha picada no graneleiro. Já se estiver fechada, surgem muitos grãos na retrilha e grãos quebrados no tanque graneleiro.
O ventilador cria uma corrente de ar nas peneiras inferior e superior para limpar a passagem dos grãos. Se o fluxo de ar for muito forte, o grão é erguido da peneira superior. Já se o fluxo for fraco, as peneiras ficam sujas de palha, impedindo que os grãos caiam. Em ambos os casos, ocorrem perdas de grãos. Para proporcionarmos uma corrente de ar adequada, utilizamos as aletas direcionadoras para direcionar a corrente mais para frente ou para trás das peneiras.
Anderson Wolf Machado - Engenheiro Agrônomo
Referências:
BORÉM, A.; SCHEEREN, P. L. Trigo: do Plantio à Colheita. [S. l.]: Universidade Federal de Viçosa, 2015.
JORIS, H. A. W. et al. Informações técnicas para trigo e triticale: Safra 2022. 14ª Reunião da Comissão Brasileira de Pesquisa de TRIGO E TRITICALE, Fundação ABC e Biotrigo Genética, ed. 1, 2022.
PIRES, J. L. F.; VARGAS, L.; CUNHA, G. R. da. Trigo no Brasil: bases para produção competitiva e sustentável. [S. l.: s. n.], 2011.
VAS, F.; HARRISON, H. The effect of selected threshing parameters on kernel damage and threshibility of wheat. Canadian Agricultural Engineering, Ottawa, V. 11, n. 2, p. 83-87, 91, 1969.